基于视觉轮廓反馈的切丝机控制方法及装置
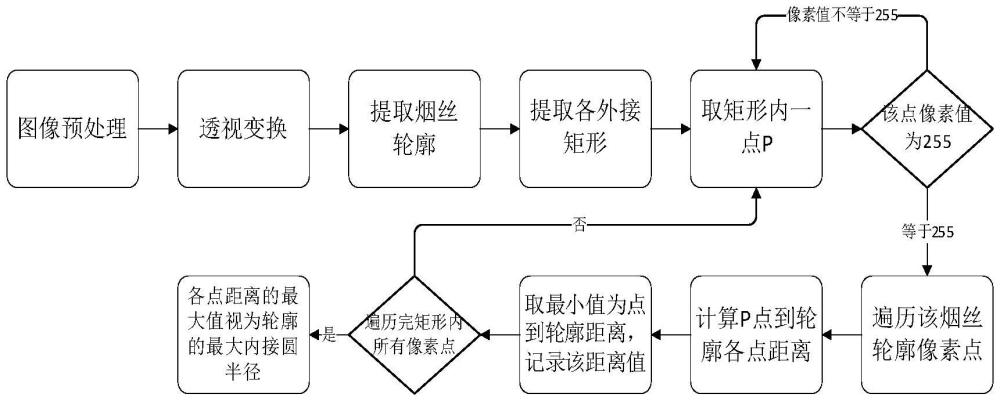
本发明涉及烟梗切丝领域,特别是一种基于视觉轮廓反馈的切丝机控制方法及装置。
背景技术:
1、在再造梗丝生产线中,烟梗切丝是极为重要的一环,它直接改变了烟梗的物理形态,决定了梗丝的尺寸和形状,进而影响到烟草的燃烧性能和最终的用户感官体验。
2、市场上常见的切丝机包括上下式、旋转式和滚刀式。上下式切丝机是较早使用的切丝设备,但因为无法保证整丝率,逐渐被旋转式和滚刀式切丝机所取代。旋转式切丝机相对于滚刀式切丝机因为机械结构设计不同,前者依靠刀片快速旋转完成切割,切割压力更大,组件提前磨损;滚刀式切丝机是通过圆柱形滚刀的旋转完成切削,组件寿命长、切割更稳定、整碎度适宜。
3、关于切丝宽度的精确控制,已成为烟草加工领域内广泛关注的研究焦点。精确的切丝宽度不仅关乎成品烟草的整丝率,还直接影响卷烟的结构和感官体验。现有技术中已经从多个角度探索改进切丝技术。
4、一是制丝工艺参数调整。例如,对影响切丝宽度的可能因素进行数据分析,需要及时调整过程工艺点(烟叶含水率、刀辊转速、车间湿度)偏差才能保障切丝宽度的合格与稳定。例如,刀门压力和刀门高度对切丝宽度均有显著影响,优化参数后,可以保证切丝宽度稳定。
5、二是切丝机械结构的优化设计。此类研究较多,例如,通过对切丝工艺及设备结构进行优化,对纵切辊剪刃侧隙进行了优化,提高了制丝质量。例如,在同一滚切过程中具多个切削角(径向前角、卸荷角和间隙角)的滚刀设计,通过机械结构的优化,有效提高切削能力。例如,在进给杆上加工滑块槽,使滑块在槽中滑动时带动回转体旋转,由回转体驱动推刀块运动完成进刀,实现切丝过程中单次进刀量恒定。例如,为了更好地解决旋切刀叶片结构的合理设计以及切烟粒度比例的有效控制问题,建立了一种具有凹凸边和边间凹槽的clsc刀片设计方法,并提供了具体的结构方案。
6、三是控制方式升级。例如,通过在出口加装激光测距仪,实时检测出口物料高度,通过高度估算流量,作为控制的反馈信号实现了切丝段流量闭环控制。因为中间涉及多次换算,所以精度有限。例如,西门子公司simotion运动控制系统在烟草切丝机中的应用。
7、但当前绝大部分制丝线上,切丝段流量控制采用的是人工控制,切丝工凭经验调整切丝机刀盘(刀辊)转速,无法反馈切丝宽度是否满足工艺要求。
技术实现思路
1、为了解决上述技术问题,本发明提出了一种基于视觉轮廓反馈的切丝机控制方法及装置。
2、实现本发明目的的技术解决方案为:
3、第一方面,本发明提供了一种基于视觉轮廓反馈的切丝机控制方法,包括以下步骤:
4、构建切丝机机理模型,确定切丝机的初始工作参数;
5、采用机器视觉技术将所切丝机作用下的切丝图像进行视觉反馈,得到切丝宽度;
6、其中,所述机器视觉技术包括:在获得的切丝轮廓区域的外接矩形内遍历像素点,计算各像素点到轮廓像素点的距离,取最小值视为该点到轮廓的距离并以此求出像素宽度;
7、基于切丝宽度实时调整所述切丝机的工作参数。
8、在某些实施例中,所述构建切丝机机理模型具体包括以下步骤:
9、刀辊上均匀分布有n片切丝刀片,那么刀辊每旋转一转,切丝刀片切割烟饼n次,t时间内共切割烟饼的次数为:
10、n=n×t×ω×60/2π
11、式中:ω为刀辊驱动电机角速度;
12、每次切割的烟饼宽度定义为烟丝宽度:
13、
14、其中,n是t内共切割烟饼的次数。
15、在某些实施例中,切丝宽度测量包括以下步骤:
16、步骤1,将获取的烟丝的图像进行预处理;
17、步骤2,将步骤1中的图像进行透视变换;
18、步骤3,对步骤2中透视变换后的图像提取各个烟丝轮廓;
19、步骤4,提取步骤3中图像的烟丝轮廓的外接矩形;
20、步骤5,取步骤4中图像矩形内一点p;
21、步骤6,若该p点像素值为阈值,则进入步骤7,否则返回步骤5;
22、步骤7,遍历烟丝轮廓像素点;
23、步骤8,计算p点到各烟丝轮廓像素点距离;
24、步骤9,取p点到烟丝轮廓像素点距离距离中的最小值,记录该距离值:,
25、步骤10,若遍历完矩形内所有烟丝轮廓像素点,则进入步骤11,否则返回步骤5;
26、步骤11,各点距离值的最大值视为轮廓的最大内接圆半径,而最大内接圆半径的两倍则为烟丝宽度。
27、在某些实施例中,将获取的烟丝的图像进行预处理具体包括以下步骤:
28、步骤11,将烟丝的图像进行灰度化,突出显示图像的轮廓和形状;
29、步骤12,对步骤11中灰度化后的图像进行自适应二值化,增强图像中不同区域的对比度,将灰度图像转化为二值图像;
30、步骤13,对步骤12中的二值图像进行膨胀处理;
31、步骤14,对步骤13中的膨胀处理后的图像进行滤波处理;
32、步骤15,对步骤14中的滤波处理后的图像进行腐蚀处理,得到最终的预处理图像。
33、在某些实施例中,还包括:构建关于切丝机机理中电机的电机模型。
34、在某些实施例中,所述电机模型采用pmsm系统的数学模型;
35、本数学模型采用非级联结构取代传统的速度环和电流环级联结构,该pmsm的数学模型可以表示为:
36、
37、
38、ym(t)=ω(t-τ)
39、y(t)=ω(t)
40、其中τ是时延;ω是角速度;iq为q轴定子电流;uq为q轴定子电压;np是极点对数;lsm、rsm、jm、ψfm、bm为电机参数标称值;ym(t)是时延测量输出;y(t)是无时延测量输出。
41、将原系统转换为如下形式,状态方程如下:
42、
43、其中x(t)是状态,u(t)是控制输入,a,b,c是适当维度的系统矩阵;
44、在某些实施例中,还包括:基于电机模型设置时延观测器和控制器。
45、在某些实施例中,时延观测器设置如下:
46、
47、其中和是ω(t)和iq(t)的观测值,l是观测器增益;将以上时延观测器离散可得:
48、z(k+1)=fz(k)+gu(k-d)+hym(k)
49、其中d=τ/t(文中t均简化处理,即k+1=kt+t);控制器的形式如下:
50、u(k)=-kz(k)
51、其中k是控制器的增益,其中
52、第二方面,本发明提供一种基于视觉轮廓反馈的切丝机控制装置,包括存储器和一个或多个处理器,所述存储器中存储有可执行代码,其特征在于,所述处理器执行所述可执行代码时,用于实现所述的基于视觉轮廓反馈的切丝机控制方法。
53、本发明与现有技术相比,其显著优点是:
54、本发明基于视觉轮廓反馈的切丝机控制方法及装置捕捉切丝过程中切丝的即时图像,并通过机器视觉技术实时分析梗丝的宽度和质量。然而,使用高速视觉技术监控和反馈过程中不可避免地会引入一定的时延,这一时延可能影响切丝机的实时调整能力。为了克服这一挑战,本发明进一步开发了先进的算法来预测和补偿这些时延,确保控制系统能够快速响应梗丝尺寸的变化。通过将视觉反馈信息直接映射到运动控制指令,本发明不仅提高了切丝宽度的控制精度,还显著提升了整体生产线的自动化水平和响应速度。
技术研发人员:郑庆元,邵立人,郭云均,余勇,程欣欣
技术所有人:江苏第二师范学院
备 注:该技术已申请专利,仅供学习研究,如用于商业用途,请联系技术所有人。
声 明 :此信息收集于网络,如果你是此专利的发明人不想本网站收录此信息请联系我们,我们会在第一时间删除