一种铁尾矿回收工艺的制作方法
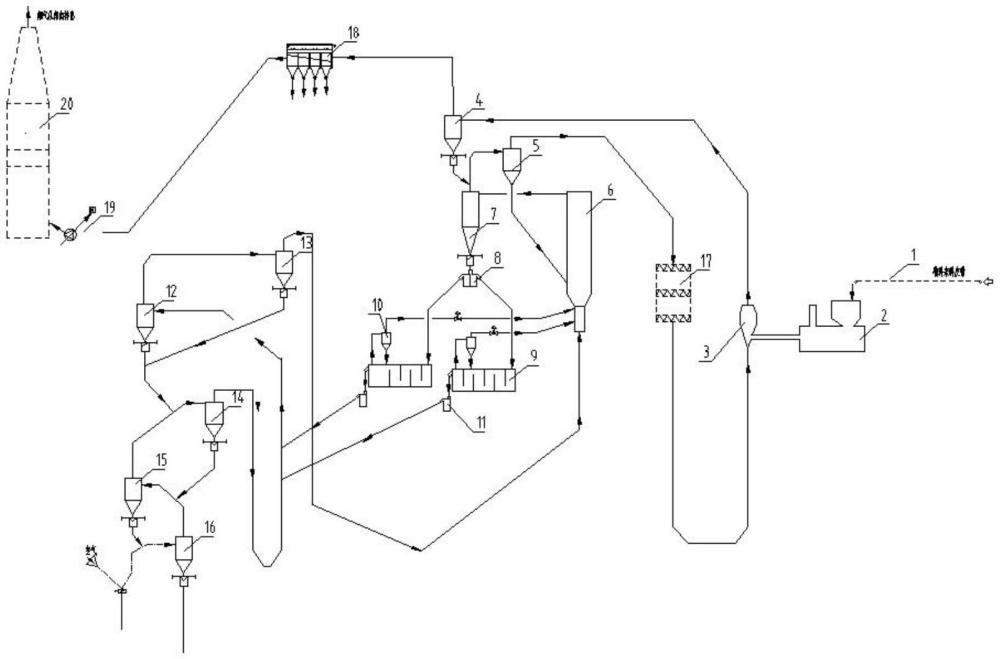
本发明涉及尾矿资源回收利用,具体为一种铁尾矿回收工艺。
背景技术:
1、铁尾矿是选矿后的废弃物,是工业固体废弃物的主要组成部分。据不完全统计,全世界每年排出的尾矿及废石在100亿t以上。我国现有8000多个国营矿山和11万多个乡镇集体矿山,堆存的尾矿量近50亿t,年排出尾矿量高达5亿t以上,其中黑色冶金矿山年排放尾矿量达1.5亿t。
2、我国的尾矿综合利用率只有7%,堆存的铁尾矿量高达十几亿吨,占全部尾矿堆存总量的近1/3。将尾矿堆存不仅需要占用大量土地,给周围的生态环境造成很大的伤害,而且要投入各自处理和维护费用。而进行尾矿资源的综合回收与利用,不仅可以充分利用矿产资源,扩大矿产资源利用范围,延长矿山服务年限;也是治理污染、保护生态的重要手段;还可以节省大量的土地和资金,解决就业问题,造福于人类社会,实现资源效益、经济效益、社会效益和环境效益的有效统一。
3、我国每年产生铁尾矿1.1亿t以上,尾矿全铁品位平均在11%以上。如果从铁尾矿中回收的铁精矿按品位60%、产率2%~3%计算,每年可回收铁精矿300~400万t,相当于一个大型铁矿企业选矿厂的产量。铁尾矿细度-0.074mm的占50%左右,相比从原生低品位铁矿石中回收铁,磨矿成本可节约近70%。因此对尾矿资源进行综合利用研究,提取尾矿中的目的性矿物,在现有科技水平下,兼顾经济合理性,最大限度地利用尾矿资源,变废为宝,既保护生态环境,又有利于企业长远发展。
4、在现有工艺方法中,对于铁尾矿的再选,主要采用磨矿后强磁选、重选以及它们与浮选的联合工艺。但这些工艺方法,要么回收指标低下,磨矿后会产生大量的微细粒次生矿泥以及大量的微细粒铁矿物,微细粒铁矿物极易在磁选、重选流程中流失,而微细粒的次生矿泥又会恶化浮选环境导致浮选指标不佳,部分工艺的回收率甚至不足10%;要么工艺流程复杂,往往是预选、磨矿、磁选、重选和浮选的多方组合,不仅投资和生产成本高,而且不利于生产操作与控制,不符合尾矿再选的生产实施要求。可见,为了充分合理地利用我国丰富的铁尾矿资源,在常规选矿工艺之外,研究并发展有效的铁尾矿再选新工艺,寻找在技术经济上合理的选矿工艺流程,无疑具有重要意义。
技术实现思路
1、本发明的目的在于提供一种铁尾矿回收工艺,采用悬浮焙烧还原加磁选进行铁尾矿资源中铁金属的回收,以解决现有技术中存在的问题。
2、为了解决上述技术问题,本发明提供如下技术方案:一种铁尾矿回收工艺,包括以下工艺步骤:
3、(1)铁尾矿的制粒
4、由皮带输送机将铁尾矿输送入摇摆式颗粒机,同时加入粘结剂,摇摆式颗粒机通过刮刀的挤压和剪切作用使物料挤过筛网变成颗粒,颗粒粒径2mm以下,制成的颗粒通过气力输送至预热脱水部分;
5、(2)铁尾矿预热脱水部分
6、将制粒后的铁尾矿采用文丘里干燥器、一级旋风预热器、二级旋风预热器预热脱水;
7、(3)铁尾矿的焙烧氧化部分
8、所述预热脱水的铁尾矿通过一级旋风加热器、二级旋风加热器加热氧化;
9、(4)铁尾矿还原槽还原
10、加热氧化后的铁尾矿通过双向锁气阀均分进入还原槽,还原槽内通入氢气及一氧化碳的混合气进行铁尾矿的还原,将不含磁性的α-fe2o3还原为带有磁性的γ-fe2o3,还原过程中漂浮的细小颗粒铁尾矿经四级旋风加热器分离,铁尾矿返回还原槽,高温烟气进入一级旋风加热器,还原后的铁尾矿由单向锁气阀输送到冷却部分;
11、(5)铁尾矿的冷却回收部分
12、铁尾矿随负压依次进入一级旋风冷却器、二级旋风冷却器、三级旋风冷却器、四级旋风冷却器,铁尾矿从400-600℃在3-5min内快速降温,由旋风冷却器气固分离,五级旋风冷却器对一级旋风冷却器未分离出的细小颗粒进行再分离,分离冷却完成后铁尾矿形成铁粉进行回收,回收后进入磁选部分;
13、(6)烟气处理部分
14、整个预热、焙烧、还原、冷却系统负压来源于烟气系统的引风机,引风机将烟气分别经脱硝反应器、布袋除尘器、脱硫塔进行烟气处理;
15、(7)铁粉的磁选
16、回收冷却后的铁粉经过再磨,磨矿至200目占比90%,进行磁选,磁选的磁场强度0.4-0.6t。
17、进一步的,步骤(1)所述粘结剂为羧甲基纤维素钠。
18、进一步的,步骤(1)所述粘结剂占铁尾矿质量5-10%。
19、进一步的,步骤(2)所述预热温度200-300℃,预热时间5-10min,系统负压10-12kpa。
20、进一步的,步骤(3)所述加热时间3-5min,加热温度600-800℃,系统负压5-8kpa。
21、进一步的,步骤(3)所述一级旋风加热器椎体部分安装有燃烧站,燃烧天然气提供热源。
22、进一步的,步骤(4)所述还原温度500-700℃,还原停留时间1-2h。
23、进一步的,步骤(6)所述处理后烟气粉尘浓度低于40g/nm3,so2含量低于20mg/m3,氮氧化物含量低于15mg/m3。
24、与现有技术相比,本发明所达到的有益效果是:
25、(1)本发明对铁尾矿中的铁元素进行回收,减少了铁尾矿堆存的环境污染,同时回收的金属可重复利用,创造了经济价值。
26、(2)本发明采用火法焙烧还原,增加了铁元素的磁性,使铁元素回收率更高,可提高20-30%的回收率。
27、(3)本发明采用火法焙烧还原,减少了铁尾矿再选过程中的水资源消耗。
28、(4)本发明采用焙烧、还原、磁选,工艺流程简单,降低了投资和生产成本,而且利于生产操作与控制。
29、(5)本发明工艺中还原槽、冷却系统的热量可返回到一级旋风加热器进行重复利用,降低了能源消耗成本。
30、(6)本发明增加了原料的制粒步骤,增加了铁尾矿颗粒直径使旋风分离器还原效果更好,避免铁尾矿的重复分选,提高了系统的处理能力。
技术特征:
1.一种铁尾矿回收工艺,其特征在于,包括以下工艺步骤:
2.根据权利要求1所述的一种铁尾矿回收工艺,其特征在于,步骤(1)所述粘结剂为羧甲基纤维素钠。
3.根据权利要求1所述的一种铁尾矿回收工艺,其特征在于,步骤(1)所述粘结剂占铁尾矿质量5-10%。
4.根据权利要求1所述的一种铁尾矿回收工艺,其特征在于,步骤(2)所述预热温度200-300℃,预热时间5-10min,系统负压10-12kpa。
5.根据权利要求1所述的一种铁尾矿回收工艺,其特征在于,步骤(3)所述加热时间3-5min,加热温度600-800℃,系统负压5-8kpa。
6.根据权利要求1所述的一种铁尾矿回收工艺,其特征在于,步骤(3)所述一级旋风加热器椎体部分安装有燃烧站,燃烧天然气提供热源。
7.根据权利要求1所述的一种铁尾矿回收工艺,其特征在于,步骤(4)所述还原温度500-700℃,还原停留时间1-2h。
8.根据权利要求1所述的一种铁尾矿回收工艺,其特征在于,步骤(6)所述处理后烟气粉尘浓度低于40g/nm3,so2含量低于20mg/m3,氮氧化物含量低于15mg/m3。
技术总结
本发明公开了一种铁尾矿回收工艺,涉及尾矿资源回收利用技术领。本发明对铁尾矿中的铁元素进行回收,减少了铁尾矿堆存的环境污染,同时回收的金属可重复利用,创造了经济价值,并采用火法焙烧还原,减少了铁尾矿再选过程中的水资源消耗,增加了铁元素的磁性,使铁元素回收率更高,可提高20‑30%的回收率,在此基础上,采用焙烧、还原、磁选,工艺流程简单,降低了投资和生产成本,而且利于生产操作与控制,同时,本发明工艺中还原槽、冷却系统的热量可返回到一级旋风加热器进行重复利用,降低了能源消耗成本。本发明增加了原料的制粒步骤,增加了铁尾矿颗粒直径使旋风分离器还原效果更好,避免铁尾矿的重复分选,提高了系统的处理能力。
技术研发人员:王胜友,崔玉辉,朱宁
受保护的技术使用者:扬州逢石矿冶科技有限公司
技术研发日:
技术公布日:2024/11/18
技术研发人员:王胜友,崔玉辉,朱宁
技术所有人:扬州逢石矿冶科技有限公司
备 注:该技术已申请专利,仅供学习研究,如用于商业用途,请联系技术所有人。
声 明 :此信息收集于网络,如果你是此专利的发明人不想本网站收录此信息请联系我们,我们会在第一时间删除